Turning the use of our products on its head
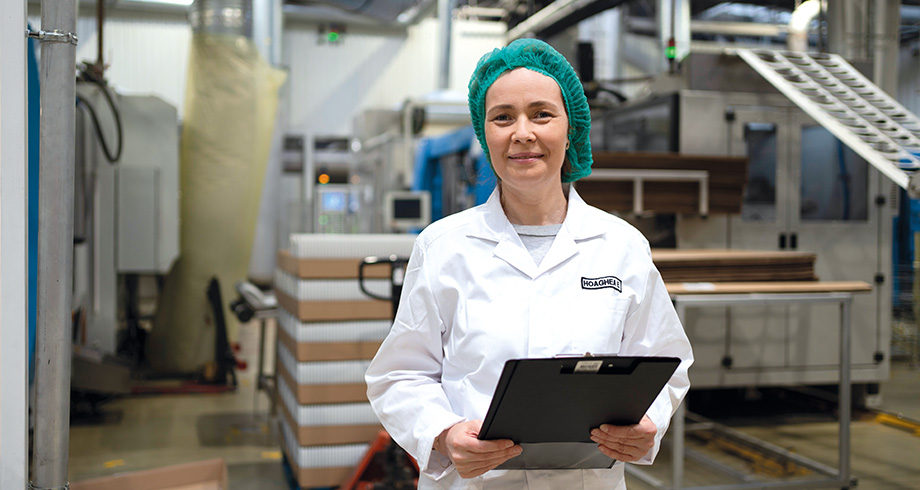
“At Greiner Packaging, we also produce plastic packaging that can be reused multiple times and is therefore particularly in line with our sustainability vision.”
The future must be circular. To achieve this, all products will be put to the test. Do single-use products have to remain single-use products? Can a product be repurposed and used for longer? Can we as manufacturers do anything else to make the use of our products sustainable? These are just some of the questions we are asking ourselves. In many cases, some of which we will illustrate here, we have already found answers and made changes. In other areas, we are still researching, developing and thinking.
Greiner Bio-One
A tube in the fight against the pandemic
Since the onset of the coronavirus pandemic, at the latest, we have all been aware that a healthy life cannot be taken for granted. Covid tests have been an irreplaceable part of our repertoire of measures to tackle the Covid-19 pandemic since the start of 2020. To meet the immense rise in demand on account of this medical challenge, Greiner Bio-One very quickly developed the VACUETTE® Virus Stabilization Tube. This 3 ml tube made from PET plastic makes it easy to handle, safely transport and store Covid-19 test samples. The samples taken from the nose or mouth/throat area of the person being tested are put into the tube and sent to the laboratory for a PCR analysis. In turn, Greiner Bio-One’s VACUETTE® Blood Collection Tube (e.g. serum or EDTA tube) is used to test whether a person has formed antibodies against SARS-CoV-2. In combination with the products from the VACUETTE® Transport Line, the sample material arrives, sealed, at the laboratory to be tested for SARS-CoV-2.
Greiner Packaging
Innovative refill solution to replace disposable containers
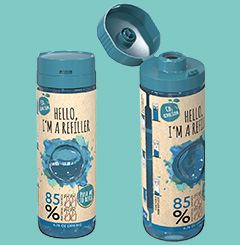
Reusing products multiple times is sustainable. Greiner Packaging developed a new refill concept for plastic spray bottles so that consumers do not need to buy a new bottle of household cleaner every time. This way, reusing and refilling spray bottles can become the new normal. The new refill bottle is made out of HDPE, PP or PET material, meets all current market requirements and saves four plastic spray bottles per bottle, including the top piece. The material savings increase to up to 85 percent over the intelligent refill cycle. Replacing 20 million standard spray bottles with our multi-use, refill solution would save up to 1,000 tonnes of plastic every year. We believe it is extremely important for the overall packaging to be recyclable as best possible. This approach is also consistently adopted when selecting the material and decoration and customers receive individual advice about the circular economy. Greiner Packaging also recommends choosing a compatible material for decorative labels that ensures maximum recyclability.
Circular economy: the example of school milk
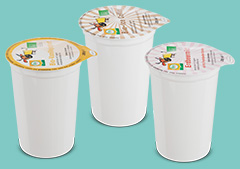
Pupils in Upper Austria learn about how the circular economy works in day-to-day life as part of a school milk project developed by us. PETMAN GmbH, an Upper Austrian company that specializes in processing and developing new applications for PET, and the farmer Johannes Strobl approached us with a desire to produce a PET cup for school milk. Our aim for the project was for it to be 100 percent recyclable and form a closed cycle. We also had to ensure that it meets all rules and regulations of the European Food Safety Authority (EFSA). At the end of 2020, we achieved our goal: The first truckload of cups made entirely from r-PET (recycled PET) was delivered to co-creator Strobl and to other school milk farmers. After pupils’ milk break, the farmers collect the used cups and take them back to their farms, where they are collected again in exchange for new cups, shredded, washed and processed into new PET film.
Reusable lids keep yogurt fresh – and much more
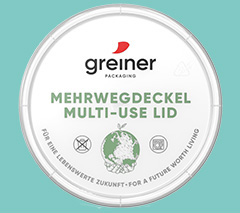
Most food and non-food packaging is used only once before, ideally, ending up in the recycling. At Greiner Packaging, however, we also produce plastic packaging that can be reused multiple times and is therefore particularly in line with our sustainability vision. For example, we have developed a reusable, dishwasher-safe snap-on lid. This can be reused for new yogurt pots, keeping the yogurt fresh and ensuring that it does not lose its taste. Our reusable lids are not only practical, they also help reduce plastic. They are also a way of avoiding large amounts of waste – once the pots are empty, our lids do not end up in the garbage.
NEVEON
Sitting intelligently
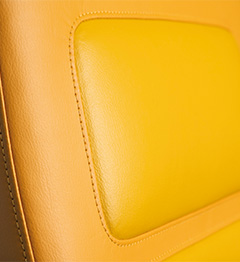
Rethinking products is part of NEVEON’s DNA. Developing an intelligent aircraft seat demonstrates this. The seat systems, with are fitted with sensor electronics, allow predictive, targeted maintenance for parts that have worn out. This increases the lifetime of the seat cushions and so only seats that are actually faulty or worn out need to be replaced. By reducing waste, this smart solution is a win for the environment. As maintenance work can be done more selectively, aircraft downtime is also reduced. Last but not least, the seat also helps improve passengers’ physical wellbeing. The sensors built into the seats generate data that can be used to analyze passengers’ sitting positions and subsequently to prevent incorrect posture.
Extending the lifetime of foams
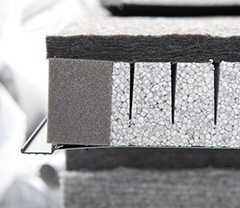
Extending the lifetime of products is good for the environment and good for society. All foams have a defined lifetime, which is affected by factors such as the weather, UV radiation and humidity. At NEVEON, we are committed to durability and therefore to optimizing this lifetime. xdura® is one example of this. This foam has allowed us to develop a durable and exceptionally stable foam that does not lose its shape even after many years of use. For example, the foam is tear-resistant. xdura® is also soft, supple and elastic – exactly what you want from a high-quality foam. With a far longer lifetime compared to other foams, it is also excellent in meeting our desire for greater sustainability.
Lighter aircraft, trains and cars
Comfortable, light, environmentally friendly – NEVEON’s seat cushion is all of these three things. It combines the highest levels of comfort with minimal weight and, at the same time, closes the material cycle. This sustainability coup is based on a special knitting technology that uses recyclable or biodegradable fibers and technical zones of varying elasticity. Compared to traditional foam solutions, knitted seat systems reduce weight by up to 30 percent. Using NEVEON seat cushions in airliners reduces their weight by more than half a tonne. An Intercity train would be almost six tonnes lighter and a five-seater car 75 kilograms lighter. As well as saving energy when operating the mode of transport fitted out with this seat technology, there is also huge savings potential for resources and energy at all stages of manufacturing and supply logistics. Customized production also eliminates production waste. At the end of their lifetime, the use of sustainable materials (from renewable raw materials) means that the seats can be recycled or, in theory, biodegraded.
Greiner Extrusion
Maximum material consumption savings
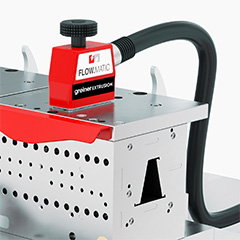
The DIGI.LINE developed by Greiner Extrusion regulates the extrusion process digitally and optimally in real time, ensuring not only exact geometry of the profile but also making it possible to produce this close to our lower tolerance limits. DIGI.LINE’s innovative features also accelerate the start-up process and lower the error rate, dramatically cutting back waste and in turn reducing material consumption. The automated melt flow control FLOW.MATIC also ensures exact profile geometry. FLOW.MATIC measures the filling level of the individual full profile sections and, together with the FLOW.CONTROL nozzle function, closes a control loop. The result is extremely constant profile dimensions – without any manual intervention. The settings can be reproduced at any time using DIGI.CONTROL. The profile weight is monitored by the precise DIGI.SCALE in-line profile weighing system, while the WEIGHT.MATIC control loop permanently controls the haul-off speed. This, in combination with FLOW.MATIC, enables production close to the lowest weight tolerance. Trends in profile weight development can also be called up at any time using the permanent data recording. The intuitive 15” DIGI.CONTROL centrally controls the entire extrusion process. For complete reproducibility and a fast start-up process, the recipes are stored with the set processing conditions and are available for future production. This ensures an automated and error-free reproduction of the process parameters in subsequent productions. Thanks to this technology, DIGI.LINE reduces typical profile weights by almost three percent, considerably reducing the amount of material used in connection with this.